Innovating Metals: Andrew Wessman on Sustainable Solutions in Engineering and Education
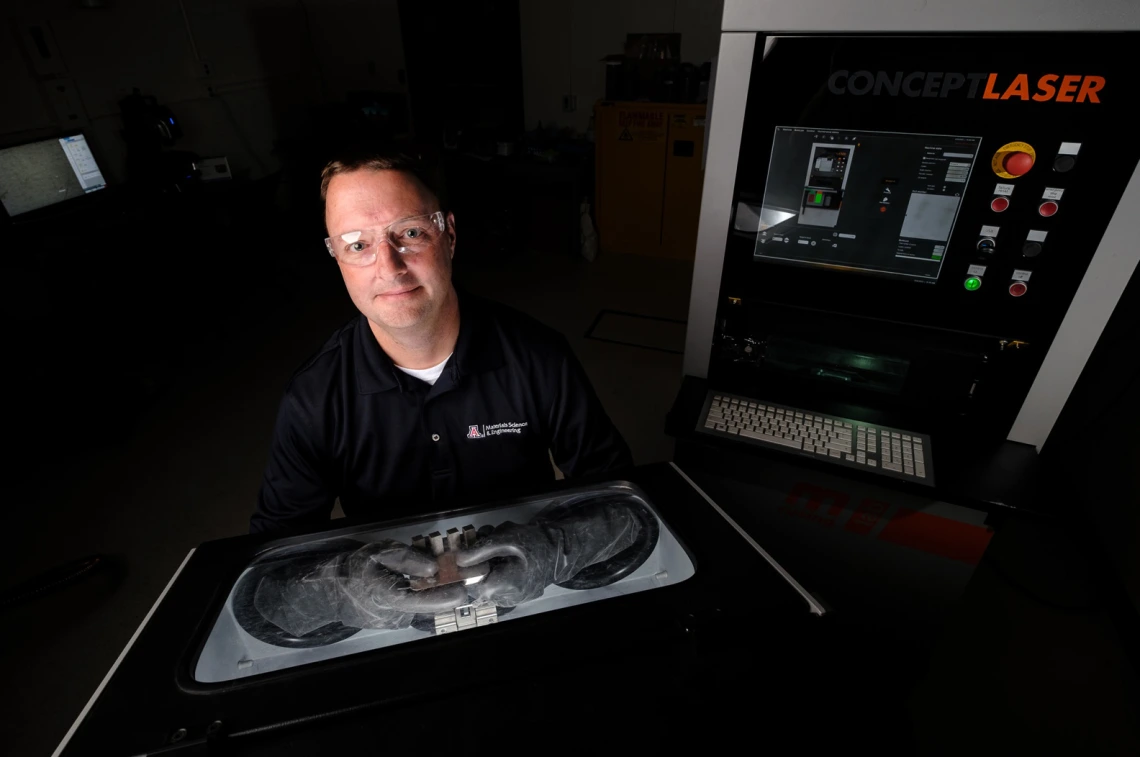
Andrew Wessman is an assistant professor in the materials science and engineering department at the University of Arizona. He joined the department in August 2019 after 14 years at GE, where he worked at GE Aviation and later GE Additive. His research focuses on polycrystalline nickel superalloys for turbine engines and high-temperature materials for additive manufacturing. Wessman holds BS and MS degrees in metallurgical engineering from the University of Utah and a PhD in materials science from the University of Cincinnati.
What inspired you to pursue a career in engineering?
I’ve always been interested in math and science, especially chemistry and physics. My dad was an engineer, but as a full-time naval officer, he wasn’t a practicing one. However, we often talked about using science to solve problems. Cycling was what really sparked my interest in metals. I worked at a bike shop, and seeing all the different metals—steel, aluminum, titanium—got me curious about their properties. I initially studied chemical engineering, but the petrochemical focus didn’t appeal to me. I found my way to metallurgical engineering, which offered opportunities that aligned better with my interests.
What drew you to the School of Mining & Mineral Resources?
It’s a good fit for my background. I have a strong foundation in extractive metallurgy, but much of my career has been in physical metallurgy and alloy development, particularly in the jet engine industry. Joining the University of Arizona gave me the chance to reconnect with extractive metallurgy while also exploring how these processes relate to my research in physical metallurgy, manufacturing, and additive manufacturing. Working with the School allows me to collaborate with faculty across various fields to tackle broader problems, such as lifecycle management.
What drives your passion for research and teaching?
I enjoy working on projects that have real-world applications. I spent years developing materials for jet engines, and many of those materials are now used in aircraft. It’s rewarding to know that something I helped create is flying under the wing of an airplane. My research tends to have a practical focus, with an end use in mind. Teaching, which I took on mid-career, allows me to share my industry experience with students, most of whom will go into practical, industry-based roles. Helping them develop the skills they need for success is incredibly fulfilling.
What advice would you give students interested in a similar career?
Focus on the fundamentals and excel in your coursework, but also seek out practical experiences. Interacting with companies and finding internships—whether on campus or through summer programs—can be invaluable. Hands-on experience teaches you what’s critical to succeed in the industry.
How does your work address global challenges like population growth and climate change?
A lot of my work focuses on improving manufacturing processes and developing materials used in everyday products. At GE, I worked on more affordable metal alloys and ones that could increase jet engine operating temperatures, directly improving fuel efficiency and reducing carbon emissions. Now, I’m also looking at industries impacted by mining and manufacturing, particularly electrification. Electric vehicles rely on different elements, and securing enough of those materials can help reduce our reliance on a carbon-based economy. By developing processes to substitute scarce elements with more abundant ones and reclaim materials from products at the end of their life cycles, we can support sustainable growth.